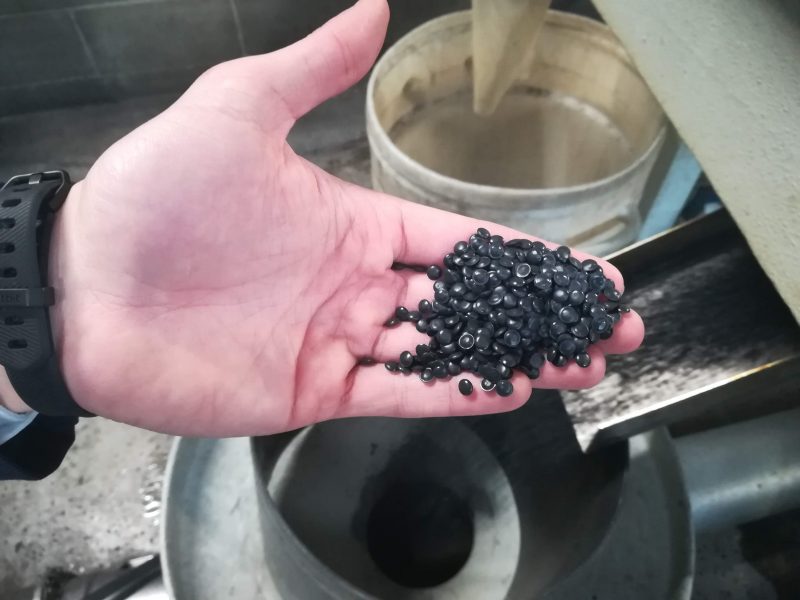
Dopo l’installazione del sistema ABMF ideato in Germania da BritAS, la produttività è cresciuta e il livello eccezionale di qualità raggiunto nella filmatura sta consentendo ad ACM, azienda milanese specializzata nel riciclaggio di materie plastiche, di acquisire nuovi clienti. Con notevoli risparmi anche sui costi di gestione.
Se per un’azienda di piccole dimensioni la qualità del prodotto finale è il fattore fondamentale per vincere la concorrenza, il caso della ACM di Turbigo (Milano), specializzata nella lavorazione delle materie plastiche e biodegradabili, fa scuola per capire come siano poi soprattutto i dettagli del processo produttivo a fare la differenza in un mercato così difficile.
La storia di quest’impresa totalmente made in Italy inizia nel 1991 e oggi, grazie a continui investimenti in macchinari e risorse umane, tenendo al centro la soddisfazione del cliente, ACM è un’azienda tecnologicamente avanzata, attenta alle tematiche ambientali come al risparmio energetico. I macchinari sono di ultima generazione e le trafile, cuore della produzione, sono tutte nuove, perché massima rapidità ed efficienza, con tendenza ad azzerare i tempi morti e restringere i tempi di consegna, mantenendo standard di qualità elevatissimi, rimangono un must.
“Lavorare molto bene è sempre stata la nostra migliore pubblicità”, spiega il titolare Luca Moroni, che abbiamo incontrato insieme a Luca Montalbetti, sales manager di Polyfilm, la società che rappresenta BritAS in Italia. “Compriamo scarti in polietilene HD e LD e biodegradabili, occupandoci di trattamento e rivendita del materiale rigenerato e operando anche in conto lavorazione. La nostra trafila è fornita da una marca leader nel settore e gli altri macchinari coprono praticamente ogni altra esigenza di rigenerazione, avendo come obiettivo flessibilità e versatilità”.
Dall’aprile 2018, come racconta Moroni, una svolta decisiva è arrivata con l’installazione nello stabilimento del filtro automatico a nastro ABMF, prodotto all’azienda tedesca BritAS Recycling-Anlagen (Gruppo NGA -Next Generation Analytics) e commercializzato in Italia da Polyfilm: “Lo utilizziamo con risultati eccezionali sulla linea di estrusione in polietilene, in attesa di sviluppi che rendano il cambiafiltro vantaggioso anche sulla nostra linea per materiali biodegradabili, dato che alte temperatura e appiccicosità costituiscono ancora piccoli ostacoli in questo secondo caso. Non utilizziamo materiali da lavaggio: siamo arrivati a un passaggio superiore partendo da materiali da ripasso, già lavorati, o da diretta, quindi pulitissimi, ben imballati e provenienti da scarti di altre aziende, non da piattaforme come i centri di raccolta. Produciamo solo filmatura, per cui il materiale, di analoga provenienza, deve essere pulitissimo, al contrario di quanto può essere tollerato nello stampaggio. Oggi trattiamo sulle due linee di estrusione, rispettivamente, 5 tonnellate al giorno di materiale bio e 25 tonnellate di polietilene”.
I vantaggi
Grazie alla filtrazione completamente automatizzata, precisa Montalbetti, la qualità del rigranulato è uniforme e i costi d’esercizio sono ridotti al minimo. Il filtro di BritAS gestisce automaticamente la frequenza dell’intervallo di cambio, per cui la qualità del melt rimane costante durante tutta la produzione mentre le contaminazioni vengono rimosse attraverso lo spostamento della rete, con una perdita minima di materiale. Con l’aiuto di un pistone d’accumulo, l’estrusore può rimanere in funzione senza dover necessariamente diminuire la portata e la gestione è semplificata tramite un touch screen principale. Il cambio rete è previsto fino a un intervallo minimo di 2 minuti ed è possibile utilizzare contemporaneamente fino a 3 nastri filtranti.
I vantaggi derivanti dal filtro di BritAS sulla linea non bio sono numerosi, aggiunge Montalbetti: “Il filtro standard lavora con una superficie di filtraggio sempre nuova in quanto viene sostituita completamente al raggiungimento della pressione impostata. Soddisfiamo così un’ampia fascia, in costante aumento, di clienti attivi nei settori della rigenerazione post-consumo/post-industriale e nella produzione di compound, con ambiti applicativi che vanno dall’agricolo alla post-produzione , consentendo portate elevate, fino a 3-4 tonnellate/ora”.
Tra gli altri benefici derivanti dal cambiafiltro a nastro ABMF, sottolinea Moroni, c’è anzitutto l’assenza di contestazioni o lamentele da parte della clientela: soprattutto di notte gli operatori, se il materiale è sporco, sono costretti a cambiare spesso produzione e filtri, inoltre aumentando la pressione aumenta anche quella del materiale e il tutto va a discapito della qualità; col cambiafiltro tradizionale si formano poi gas e bolle nel passaggio per cui ci vuole un controllo continuo sulla produzione, mentre con l’ABMF è sufficiente, a ogni turno, inserire una nuova bobina del filtro.
Sono stati eliminati anche i fumi nel capannone, tipici quando al momento del cambio, la matarozza cade e produce gas mentre con l’ABMF lo spurgo di materiale è ridotto di 10 volte rispetto ad un filtro classico a cassetto. “La filtrazione è migliore”, continua Moroni, “e siamo riusciti persino ad abbassare la finezza di filtraggio a 90 μm. Ma la vera sorpresa è il risultato finale con materiali pulitissimi: è scomparsa ogni fastidiosa puntinatura quando invece prima, con il cambio rete, il filtro esterno riscaldato a candele bruciava, con perdita di qualità e di produzione tale da costringere a buttare fino a 2 tonnellate di materiale su ogni bilico comprato. Oggi lo scarto massimo è di 50 kg. Fino a ieri tutto questo materiale declassato doveva essere ripassato, ovviamente, con una media di 200 grammi a materozza, per cui alla fine dei tre turni di produzione quotidiani si arrivava a un totale di circa 1.500 chili da portare a macinare per il riutilizzo. Ora si arriva a uno scatolone di spurghi alla settimana, con una notevole riduzione dei costi”.
Risparmi che riguardano anche gli operatori, specifica Moroni, i quali possono quasi “dimenticarsi” del cambiafiltro dedicandosi ad attività più utili e proficue: “Abbiamo l’ABMF da quasi un anno ormai e la produttività della linea è aumentata del 20%, così come continuano ad aggiungersi nuovi clienti entusiasti della purezza dei colori ottenuti. In sostanza, abbiamo ottenuto meno cambi di lavorazione e passaggi vari, anche perché il materiale fornito ha già un filtraggio di 200 micron; minori temperature, pressioni e usura, con risparmi sulla gestione e maggiore qualità finale, quando ieri a volte interi camion tornavano indietro perché ci si era dimenticati di cambiare il filtro rovinando la partita. E se prima pagavamo le reti saldate in doppio da 309 mm sfruttando due terzi per ogni metro comprato e scartando il resto, adesso siamo in grado di utilizzare tutta la superficie della rete prodotta : abbiamo calcolato da aprile a dicembre dell’anno scorso un risparmio di ben 6mila euro con i soli filtri, per cui anche se l’investimento può apparire impegnativo, in realtà è ammortizzabile in un paio d’anni”.
A misura di produzione
Le taglie del cambiafiltro variano in base alla produzione: le superfici filtranti proposte sono di 570, 750, 1050 (la più difffusa), fino ai 1600 centimetri quadrati di recente introduzione nel catalogo di BritAS. “Variano anche le dimensioni del pistone laterale, a seconda del grado di contaminazione e della portata dell’estrusore”, spiega Montalbetti.
Un altro vantaggio fondamentale dell’ABMF è l’assenza di manutenzione: “Mi sono limitato”, conclude Moroni, “a far venire inizialmente in sede i tecnici tedeschi per apprendere tutti i segreti del sistema di filtrazione. La continuità delle lavorazioni ha già portato a un aumento di fatturato del 25% e per reperire materiali di qualità e puliti basta essere corretti con i fornitori. Ritengo quindi che i cambiafiltri automatici di BritAS rappresentino il trend per il futuro e attendo con fiducia analoghe innovazioni perfezionate per i biodegradabili, una volta superati i problemi derivanti dal mercato esterno, condizionato ancora dall’accoppiamento di materiali poco compatibili con la rigenerazione. La mission di ACM per il futuro rimane in ogni caso quella di proseguire nella nostra tradizionale politica volta alla ricerca della massima qualità”.
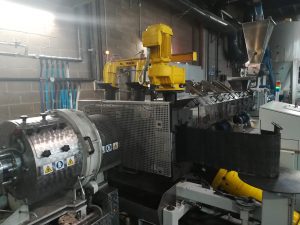
La linea di estrusione installata presso ACM equipaggiata con il cambiafiltro BritAS ABMF
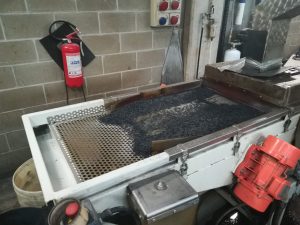
I granuli ottenuti dopo a lavorazione con il cambiafiltri BritAS
Condividi l'articolo
Scegli su quale Social Network vuoi condividere