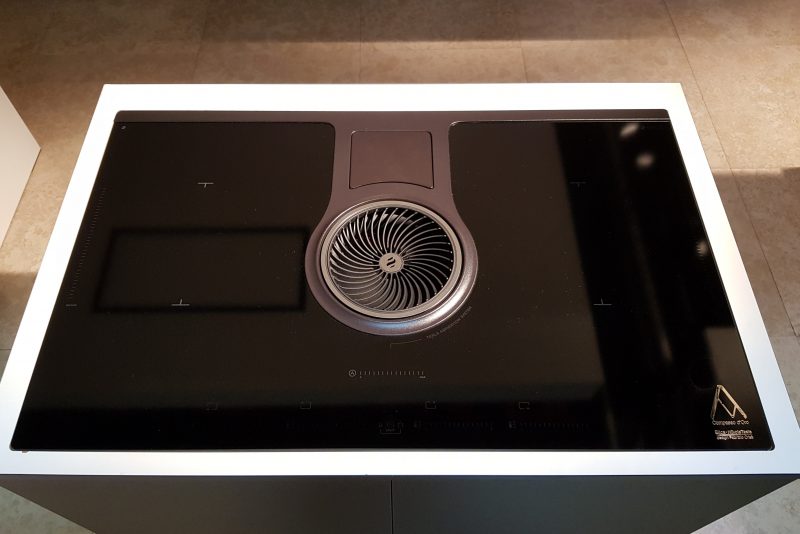
Strategie di metal replacement: il caso studio Nikolatesla di Elica, azienda costruttrice di cappe per cucina. Sostituzione di acciai con polimeri caricati ad alte prestazioni per un porta filtri ceramici integrato nel piano aspirante.
di Ubaldo Spina
Esistono, nella vita delle imprese manifatturiere, piccole sfide generate all’interno dei processi di sviluppo dei prodotti industriali. L’osservazione, la naturale propensione al perfezionamento dei componenti di chi opera con standard di qualità elevati, la capacità e l’intuizione dei progettisti portano spesso a generare innovazioni che in molti casi potrebbero essere considerate superflue ma che, alla lunga, decretano il successo di alcuni prodotti sia dal punto di vista tecnico che economico. Elica S.p.A., aziende leader mondiale nel settore delle cappe da cucina con quartier generale nella operosa Fabriano, presenta nel 2016 il suo primo piano aspirante, battezzato Nikotesla: un’architettura di prodotto completamente nuova narrata da un design pulito e ricercato al tempo stesso. Il piano è stato progettato in una logica di interazione user-friendly, sia nello sviluppo delle interfacce tattili che nel posizionamento e interazione con le interfacce fisiche connesse ai sistemi di monitoraggio e sostituzione dei filtri.
Ed è qui che si innesca un esempio perfetto di Design for Manufacturing, quella fase che Ulrich & Eppinger considerano di fondamentale importanza in cui si analizzano i driver di costo e i vincoli del processo produttivo, dove si attuano le strategie di semplificazione dei componenti e operazioni in grado di ridurre costi di produzione e di assemblaggio al tempo stesso.
Il piano, alle spalle del filtro grassi (nella parte opposta al lato utente), presenta un vano con coperchio e protezione dal quale è possibile accedere e sostituire i filtri odori ceramici. Si tratta di 4 blocchi (ciascuno con 4 filtri) rimuovibili attraverso una pratica cinghia. Il prototipo di porta filtri, un frame metallico[3] sviluppato in prima battuta per assolvere geometricamente la sua funzione, innesca fin da subito una serie di considerazioni, alcune delle quali portano il team di sviluppo a tracciare possibili criticità o interventi di ottimizzazione:
- necessità di un’estetica più professionale;
- necessità di eliminazione di rivetti e pieghe che possono ostruire l’inserimento e l’estrazione dei filtri;
- necessità di privare il componente di bordi taglienti;
- possibilità di sostituire i filtri ceramici;
- necessità di ridurre il costo del componente.
L’unico vantaggio che sembra possedere il frame metallico è quello di poter prelevare i filtri dalla loro sede mediante un magnete. Nonostante il componente sia inglobato nel vano (e quindi non soggetto a valutazione estetica da parte del cliente finale) e nonostante la durata media di 16 unità di filtri (4 blocchi) sia di circa 4 anni, Elica si approccia al problema come se il frame fosse un componente di primaria importanza per il successo del piano Nikolatesla. Si decide quindi di procedere con l’avvio di un’attività di metal replacement, cercando in un polimero PPS caricato con metallo la principale alternativa per garantire semplicità di smontaggio e caratteristiche tecniche avanzate.
I vincoli principali in grado di ostacolare la riprogettazione nascono principalmente dalle condizioni di esercizio in cui il polimero sarà costretto ad operare, ovvero:
- resistenza alle alte temperature: i filtri odori ceramici possono essere rigenerati ogni 2/3 mesi in forno per una durata variabile (da 30 a 120 minuti) in un range di temperatura da 150° C a 200° C dipendente delle modalità di cottura e dalla frequenza di rigenerazione. Heat Distortion Temperature (D 648; HDT 1.82Mpa) >250 ° C & RTI (UL 746)> 200 ° C;
- classe di autoestinguenza V-0 (UL94).
Il redesign, come già anticipato, nonostante il moltiplicarsi delle soluzioni progettuali garantire dai processi di stampaggio dei polimeri, potrebbe comunque risultare inutile se non saranno verificate le seguenti specifiche tecniche e produttive:
- proprietà magnetiche del componente;
- contenimento dei costi in termini di materia prima e processo.
Viene avviata un’intensa e trasversale attività di scouting, basata principalmente sull’accesso a database tecnici online e sulla consultazione di una rete di fornitori preferenziali. La selezione ricade sulle resine PPS (Poliparafenilensolfuro) che presentano resistenza alle alte temperature, alta resistenza chimica, basso assorbimento d’acqua ed elevate caratteristiche meccaniche, nonchè una formulazione idonea per garantire la classe di autoestinguenza V-0. Si procede con la preparazione dei provini, placchette da 0.8mm a 3.2 mm di spessore, sottoponendo successivamente le stesse a una serie di test di validazione di seguito elencati:
- Needle Flame Test (IEC 60695-11-5).
- Glow Wire Test GWIT 550 °C (IEC 60695-2-13).
- Ball Pressure Test (IEC 60695-10-2 in addition CTL OSM/HA 72).
- Cicli termici in forno (13 cicli a 200°C, 45 minuti). Ciclo di rigenerazione standard dei filtri odori ceramici.
- Cicli termici in camera climatica (T= 90°C; Hr=80% per 8hr) + (T=23°C; Hr=50% per 16hr)] per 5 giorni; (T=23°C; Hr=50%) per 2 giorni.
- Ciclo termico in forno (250°C, 120 minuti). Per simulare un ciclo di rigenerazione errato.
Le prime risultanze sui test di omologazione del polimero, consentono di procedere con la progettazione dello stampo e del manufatto, le cui caratteristiche geometriche vengono completamente riviste rispetto al frame metallico e si riconducono allo sviluppo di un case (retropallet) monoblocco sul quale si sovrappone una cornice plastica con croce centrale a formare quattro cavità. Il retropallet sarà realizzato in PPS nero 40 FG, mentre la sola cornice sarà nello stesso materiale caricato con ossido di ferro. Rispetto allo sviluppo del frame metallico, i componenti non necessitano di lavorazioni specifiche/finitura superficiale e sono caratterizzati dall’assenza di connessioni meccaniche. Le prove dello stampo consentono l’approvazione del componente prima di sottoporlo ad ulteriori verifiche:
- verifiche dimensionali: validazione geometrica attraverso l’utilizzo di software metrologici 3D (con emissione di report dimensionali, verifica della catena delle tolleranze e delibera stampo);
- verifica delle proprietà termiche ed autoestinguenti sul componente stampato: 13 Cicli termici in forno (200°C, 45 minuti);
- Life Test e prove di assemblaggio del telaio in PPS eseguite sul prodotto finito. (8 settimane con diverse condizioni operative).
Al termine delle attività il portafiltri si presenta in tutta la sua valenza estetico-funzionale rispetto al componente da sostituire. Particolarmente rilevanti i risultati registrati in termini di:
- stabilità alle alte temperature (250°C);
- alta resistenza all’impatto;
- garanzia delle proprietà magnetiche;
- riduzione dei costi di produzione pari al 33% rispetto al componente in acciaio AISI 430.
Il progetto, sviluppato in seno al reparto di ricerca ed innovazione della R&D del gruppo Elica, ha confermato la tendenza ad utilizzare soluzioni concettualmente semplici per migliorare la qualità globale delle componenti e l’esperienza in termini di usability che il consumatore trae da oggetti con caratteristiche tecnico-estetiche proprie di device di tipo professionale. Nascondere le caratteristiche tecniche lasciando invariata la funzionalità del prodotto è da sempre uno dei dogmi dei prodotti Elica, che uniscono alte caratteristiche tecniche ad un design di prodotto basato sulla semplicità e sullo stile.
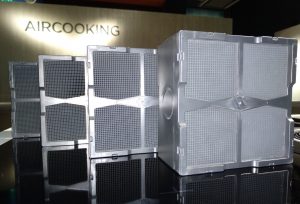
I filtri anti-odore sono accessibili dalla parte superiore del piano
Condividi l'articolo
Scegli su quale Social Network vuoi condividere