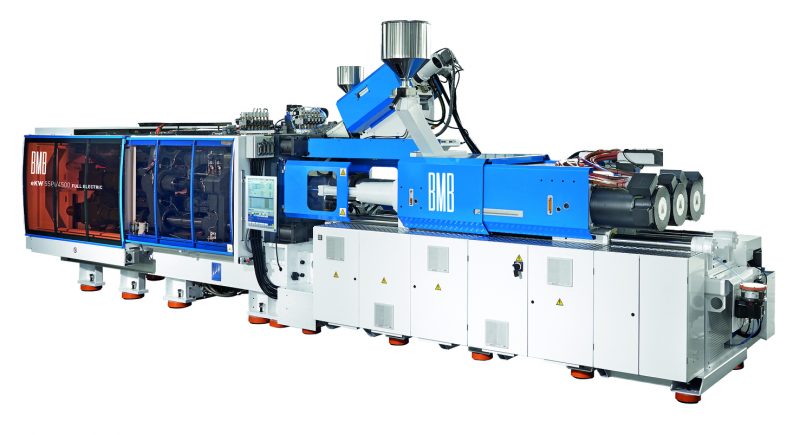
La gamma di presse per stampaggio a iniezione progettate e prodotte da BMB offre numerose soluzioni per vari campi applicativi. E più il cliente diventa esigente, più emerge una specializzazione maturata in mezzo secolo di storia che oggi permette di portare avanti, in tutto il mondo, alcuni interessanti progetti.
Con una produzione che viaggia a pieno regime e un portafoglio ordini davvero importante, l’obiettivo di BMB è continuare a crescere, soprattutto tecnologicamente, implementando la qualità e le performance della vasta gamma di presse per stampaggio a iniezione, progettate e realizzate totalmente nello stabilimento di Brescia e molto apprezzate da una clientela sempre più internazionale. Sono cinque le linee di produzione, ripartite su quattro unità produttive per un totale di oltre 40.000 metri quadrati coperti.
Grazie al completamento della nuova sede destinata all’assemblaggio e al collaudo delle macchine più grandi, l’azienda bresciana può ora contare su un miglior flusso delle attività di lavorazione interna e di magazzino componenti, concentrati in un’unica sede, capace di alimentare le linee di montaggio dei 3 stabilimenti in “just in time”. Il reparto macchine utensili ha visto aggiungersi anche nel 2021 un nuovo centro di lavoro a 6 postazioni automatizzate, capace di rifornire le linee con piani lavorati autonomamente nelle 6 facce e pronti per l’assemblaggio in linea.
La filosofia BMB è da sempre quella di conservare gelosamente la progettazione e le lavorazioni meccaniche in casa, poiché rappresentano il cuore pulsante dell’azienda e della qualità del prodotto, veri artefici della raccolta di grandi soddisfazioni sul mercato. Sia gli uffici tecnici che il reparto lavorazioni meccaniche sono in costante crescita e continueranno a dare il fondamentale contributo all’evoluzione tecnologica, sempre ricercata dal marchio BMB.
Presse per stampaggio a iniezione sempre più versatili e performanti
Tanti i progetti importanti in fase avanzata, a cominciare da alcune applicazioni accumunate da configurazioni multi-injection, ma totalmente diverse tra loro per i fini di produzione. Lo stack-mould, nato tradizionalmente per raddoppiare o quasi la produttività di un determinato articolo che ben si prestava a tale configurazione stampo, è stato oggi reinventato da BMB per la produzione di articoli molto diversi tra loro, la cui produzione può avvenire in un’unica pressa con notevoli vantaggi economici di trasformazione, iniettando autonomamente le diverse figure con taglie e parametrizzazioni indipendenti dei gruppi iniezione.
Altri progetti multi-injection vedono l’azienda bresciana coinvolta nella produzione con configurazione di 2 stampi affiancati oppure uno soltanto, in cui l’esigenza talvolta impone l’iniezione centrale singola, talvolta con 2 unità parallele e motorizzate nel loro posizionamento.
Altri scopi di fornitura richiedono presse per stampaggio a iniezione con 2 iniettori orizzontali e 2 iniettori verticali in modo tale da soddisfare l’esigenza di produrre componenti auto a 4 colori e contemporaneamente poter contare sull’utilizzo della medesima pressa nella sua configurazione classica mono-iniettore.
In tutte queste configurazioni la posizione degli iniettori è gestita elettricamente dall’ operatore, quindi memorizzabile nella ricetta dello stampo. La classica soluzione dello stack-mould trova oggi spazi maggiori anche grazie ad innovative camere calde con particolari movimenti elettrici in grado di gestire i flussi di materiali e le temperature con precisioni e risultati sorprendenti. Ecco che anche in questo caso la particolare configurazione della ginocchiera KW, brevettata da BMB, sposa in modo perfetto le esigenze di importanti spessori e pesi dello stampo, garantendone il perfetto parallelismo, senza alcuna flessione.
I progetti speciali
In contemporanea BMB continua come sempre a portare avanti i suoi progetti “speciali”, a partire da quelli chiavi in mano per l’automotive, molto spesso per la fanaleria posteriore, dove rappresenta ormai un riferimento a livello mondiale: in questo caso vengono utilizzate normalmente presse ibride o idrauliche della serie KX, con 2-4 iniettori, tavola rotante e piani magnetici, quindi sistemi di automazione con uno o più robot antropomorfi per le seconde lavorazioni a fianco pressa. Oggi le case automobilistiche puntano molto anche sulle lenti LED che richiedono determinati accorgimenti del gruppo di iniezione, quindi l’aggiunta di additivi gassosi durante la plastificazione per garantire la necessaria trasparenza di cui si deve avvalere necessariamente il prodotto.
I progetti chiavi in mano dell’elettrodomestico stanno vivendo oggi un momento davvero importante per BMB. Anche questo comparto, come il packaging e il casalingo, sta vivendo infatti un momento di gloria. Forse la pandemia e il necessario “rimanere a casa” hanno contribuito alla trasformazione della propria abitazione con nuovi oggetti, nuovi elettrodomestici e corse al supermercato, dove il packaging riciclabile la fa da padrone. Un’applicazione chiavi in mano molto interessante che BMB sta portando avanti in partnership con un cliente molto importante riguarda la nuova concezione di fare elettrodomestici. L’elettrodomestico oggi non è più solamente di alleggerimento ai lavori domestici, ma deve contribuire al miglioramento dello stile di vita, sottostare a normative e funzioni molto evolute; queste ristrette linee guida impongono al fornitore di progettare e produrre in modo nuovo, ecosostenibile, dalla progettazione dei componenti plastici, al tipo di materiale, alla riciclabilità e rintracciabilità, dove l’unica strada è rappresentata da isole di lavoro integrate e capaci di rispondere a tutte queste esigenze in ottica 4.0. Solo in questo modo si possono garantire gli standard qualitativi e produttivi imposti dai grandi players dell’elettrodomestico.
Oltre alla qualità del prodotto e all’affidabilità delle presse per stampaggio a iniezione Hybrid qui si aggiunge naturalmente l’esperienza e la capacità di guardare a 360°, perché la pressa è ora una parte importante del mosaico, ma le sue caratteristiche e performance devono sposare quelle di altri soggetti di alta tecnologia che insieme alla pressa stessa costituisco la cella di lavoro, capace di generare un prodotto finito, controllato e pronto per l’assemblaggio al costo più basso possibile. L’impresa bresciana oggi è anche questo e sempre più spesso si trova a sviluppare soluzioni che richiedono lavoro in team e determinazione a voler sempre raggiungere l’obiettivo qualitativo più ambizioso. La definizione di una cella di lavoro può richiedere molti mesi e aggiornamenti continui del lavoro di gruppo prima di raggiungere la configurazione finale.
Costruttori di presse per stampaggio a iniezione
Pur dedicandosi anche alla messa a punto di isole di produzione chiavi in mano, BMB ribadisce il suo ruolo di costruttore di presse per stampaggio a iniezione. Naturalmente, l’azienda segue le tendenze del mercato e spesso è chiamata alla fornitura della macchina speciale o completata con di sistemi ausiliari e robotizzati, ma l’attenzione e la dedizione al corretto dimensionamento e alle prestazioni della pressa per stampaggio a iniezione è sempre totale. Il core-business di BMB è garantire uno stampaggio a iniezione di alta qualità, sia esso legato al packaging per necessarie prestazioni e velocità, sia esso legato all’articolo tecnico per complessità dei materiali; questa è la ragione per cui si rivolgono al costruttore Bresciano i trasformatori che hanno bisogno di un interlocutore fidato, sempre pronto a mettersi in gioco insieme a loro con il comune obiettivo di trovare la migliore soluzione possibile.
Una gamma aggiornata
La gamma di BMB si aggiorna continuamente. Del portfolio fanno parte le presse idrauliche, sempre più rare per la verità, per lo più destinate allo stampaggio di grandi componenti. Tutta la gamma va dalle 160 fino alle 4.800 tonnellate, sia con presse a ginocchiera serie KW sia a due piani KX.
Le presse Hybrid coprono la stragrande maggioranza della domanda; il range arriva alle 2.800 tonnellate ed è ora il prodotto di punta BMB. La soluzione Hybrid è il miglior compromesso tra prestazioni e energy saving. Se da una parte infatti si può contare su quasi tutti gli azionamenti elettrici e conseguente risparmio energetico, l’iniezione idraulica sotto accumulatore preserva le prestazioni e la grande versatilità.
L’evoluzione HP della serie Hybrid copre la gamma da160 a 850 tonnellate ed è particolarmente indicata per chi produce contenitori a parete sottile dove serve una grande velocità di iniezione.
Da circa vent’anni, BMB propone le presse per stampaggio a iniezione Full Electric, che hanno dimostrato fin dall’inizio grande affidabilità per tutte le tipologie di stampaggio, essendo state progettate per il packaging, quindi per sopportare le alte prestazioni richieste, con componentistica di altissimo livello a partire dai motori diretti e viti a ricircolo di rulli, per poi incontrare il controllo CNC, tipico delle macchine utensili. Le Full Electric costituiscono la seconda linea più importante nei reparti di produzione BMB e coprono oltre il 20% della domanda, anche grazie alla vasta gamma di modelli che raggiunge oggi le 1400 tonnellate di chiusura. Una macchina sempre più richiesta dal mercato per i noti vantaggi di risparmio energetico e precisione, ma non sempre idonea a tutte le tipologie di prodotto da stampare. Alla gamma Full Electric appartengono anche le presse della serie eMC. Con un range da 125 a 200 tonnellate, destinate principalmente allo stampaggio tecnico di piccole e medie dimensioni, le presse EMC si differenziano in particolare per la natura degli azionamenti elettrici; se la serie KW vanta motori diretti e viti a ricircolazione di rulli satellite per altissime prestazioni, la più tradizionale EMC conta sul progetto più classico di motore, cinghia e riduttore, con costi più contenuti e performance di tutto rispetto. Il controllo CNC è comune a tutte le presse BMB a vantaggio della standardizzazione, dell’evoluzione software con aggiornamenti on line e di una interfaccia operatore comune a tutti i modelli.
Le tecnologie digitali per lo stampaggio a iniezione
In questa fase di emergenza sanitaria si è registrata anche forte attenzione verso le tecnologie digitali, sia riguardo all’assistenza tecnica sia riguardo al “commissioning” e BMB non si è certo tirata indietro. Da molti anni tutte le presse BMB includono di serie la connessione alla casa madre e di norma il tecnico installatore si assicura che questo avvenga sin dalla prima accensione, integrandola sia al suo network (MES), sia alla casa madre. Periodicamente, se il cliente lo desidera, viene effettuato un controllo sull’utilizzo corretto della macchina con verifica dei parametri per ottimizzazione della produttività, della qualità e dei consumi.
Tutte le macchine sono naturalmente interfacciabili Euromap 77, per la raccolta e la trasmissione dei dati, l’IoT via OPC UA. Le presse BMB possono integrare qualsiasi altro accessorio esterno come il robot, il termoregolatore, il refrigeratore e il deumidificatore posti a fianco pressa e così visualizzarne le pagine con possibilità di modifica dei parametri, trasferimento dei dati a un sistema MES per il controllo generale della cella produttiva e l’elaborazione centralizzata dei dati.
BMB sta convivendo brillantemente con questo periodo difficile per molte realtà, sia a livello produttivo che di servizio, cercando di assistere in loco i clienti ovunque, nonostante le difficoltà nel raggiungere particolari aree, fino a guidarne talvolta la messa in funzione via web, senza il tecnico installatore. Questo momento ha infine portato l’azienda a tante riflessioni che presto daranno i loro frutti per migliorare la macchina e adeguarla sempre più alle esigenze dei nuovi prodotti stampati a iniezione, riciclati, riciclabili, quindi a prevenire le possibili cause di rottura.
Case history nel settore medicale
Nel settore medicale BMB ha di recente completato un progetto di 10 macchine Full Electric con altrettanti stampi e a breve verrà avviata una produzione di siringhe da 5 e 10 ml presso un Paese emergente. Un progetto ambizioso, tutto in camera bianca, che vede il costruttore coinvolto dalla fase di movimentazione del granulo fino alla manipolazione del prodotto stampato. È stato studiato un layout particolarmente ergonomico al fine di facilitare gli operatori nel raggiungere le macchine e intervenire rapidamente in caso di necessità; sistemi acustici e visivi richiameranno facilmente l’operatore alla posizione richiesta. L’intero reparto produttivo è stato concepito in ottica 4.0, focalizzando l’attenzione contemporaneamente sugli elevati standard di qualità (in questo caso sterilità ambientale) assoluta del prodotto, risparmio energetico e affidabilità, poiché parliamo dell’Africa Sub Sahariana.
Service support
Per un’azienda capace di operare su tutti i mercati internazionali il servizio, o meglio “i servizi”, costituiscono una parte fondamentale dell’attività industriale di BMB, quella che permette di seguire da vicino i clienti, di coglierne appieno le necessità e di fidelizzarli. Filiali e agenzie di vendita BMB sparse per il mondo sono in grado di supportare i clienti sotto ogni aspetto relativo alla gestione e all’aggiornamento tecnologico delle presse.
Progettazione
La competenza di tecnici e progettisti rappresenta il plus che assicura ai clienti un servizio che va ben oltre la realizzazione del prodotto finito e che si concretizza nella soddisfazione di ogni loro esigenza. L’ufficio tecnico, diviso nei settori Meccanico, Elettronico e Software, si avvale delle più moderne tecnologie di progettazione e simulazione dei vari processi per garantire sempre la perfezione, sotto tutti i punti di vista.
Personalizzazione
Le esigenze degli stampatori non sono sempre le stesse: cambiano di continuo, adattandosi alle richieste del mercato. La capacità di fornire soluzioni “su misura”, dalla pressa all’isola di stampaggio completa, è uno dei capisaldi della strategia industriale BMB.
Costruzione e collaudo
La qualità di una pressa per stampaggio a iniezione comincia dalla sua progettazione-costruzione. Nello stabilimento BMB di Brescia sono installati centri di lavoro a controllo numerico di ultima generazione, una scelta industriale che permette di seguire ogni passo della realizzazione di una pressa, assicurando un prodotto di “qualità totale”. La costruzione è completata dal collaudo che deve garantire la piena affidabilità e l’immediata produttività della pressa.
Assistenza e teleassistenza
Grazie ad opportuni dispositivi di connessione, è possibile l’assistenza a distanza sulle presse BMB installate in ogni parte del mondo. Il servizio ricambi si segnala per la tempestività nel fornire i componenti necessari a un immediato ripristino della produzione.
L’obiettivo BMB è riuscire a far sentire il cliente vicino all’azienda, senza ostacoli, feed-back rapidi e diretti. Oggi il mondo della plastica chiede velocità e BMB cerca di offrire questo, non solo come caratteristica intrinseca delle proprie macchine per stampaggio a iniezione, ma di tutta la filiera.
a cura di Fulvio Miglio e Paolo Spinelli
Condividi l'articolo
Scegli su quale Social Network vuoi condividere