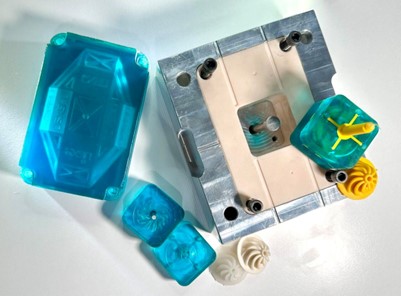
Una nuova frontiera nello sviluppo prodotto e nelle piccole serie.
Lo stampaggio a iniezione è una tecnica di produzione consolidata, ma l’introduzione di tecnologie innovative come il Freeform e l’utilizzo di materiali all’avanguardia come la resina Xmold stanno rivoluzionando il settore. In questo articolo esploreremo i vantaggi che questa combinazione offre, focalizzandoci sulle sue implicazioni per la produzione industriale.
Che cos’è lo stampaggio a iniezione FIM (Freeform Injection Molding)?
Il FIM (Freeform Injection Molding) è una variante avanzata del tradizionale processo di stampaggio a iniezione.
A differenza dei metodi convenzionali, che richiedono stampi in metallo complessi e costosi e con tempi di realizzazione lunghi, il FIM permette in fase di sviluppo prodotto di stampare ad iniezione utilizzando stampi realizzati con stampanti 3D a resina che possono essere montati su una ordinaria pressa ad iniezione per realizzare il componente nel materiale desiderato al pari di quello che otterrei con uno stampo tradizionale.
L’innovazione sta nel fatto che in questo caso il pezzo non viene estratto dallo stampo subito dopo l’iniezione ma viene estratto il tassello contenente il pezzo iniettato.
Per eseguire il demolding il tassello viene messo a bagno in un solvente dedicato che dissolve la resina Xmold con cui è fatto il tassello e alla fine del processo rimane solo il componente iniettato.
Quando e perché utilizzare FIM (Freeform Injection Molding)
- Rapidità di prototipazione: la possibilità di creare rapidamente prototipi funzionali consente di accelerare i cicli di sviluppo del prodotto e di ridurre i tempi di immissione sul mercato.
- Flessibilità di progettazione: la libertà di progettare geometrie complesse e personalizzate apre nuove possibilità creative e consente di ottimizzare la funzionalità dei componenti.
- Riduzione dei costi: l’eliminazione della necessità di stampi fisici in alluminio o zama e la riduzione dei tempi di produzione di quest’ ultimi contribuiscono a ridurre significativamente i costi complessivi.
Un esempio concreto: SPT Vilecon – Lo sviluppo di dispositivi medici richiede prototipi di qualità produttiva
I produttori di dispositivi medici devono seguire rigorosi percorsi normativi quando introducono nuovi dispositivi sul mercato.
Un dispositivo medico deve essere sicuro ed efficiente da usare per lo scopo previsto ed è compito del produttore dimostrare che un determinato dispositivo soddisfa questi requisiti essenziali.
Per farlo, i produttori devono sviluppare elaborati protocolli di test che valutano ogni aspetto della produzione e dell’utilizzo del dispositivo, e devono garantire che i test siano eseguiti in modo da rappresentare accuratamente le condizioni che si applicano per la produzione e l’utilizzo del dispositivo medico finito.
Più tardi vengono eseguiti questi test, più gravi sono le conseguenze in caso di fallimento. Le aziende produttrici di dispositivi medici sono costantemente alla ricerca di strumenti e metodi che li aiutino a migliorare i test in fase iniziale dei dispositivi per ridurre i rischi di sviluppo e i costi di rielaborazione.
SPT Vilecon lavora spesso con i siliconi, un gruppo di materiali ampiamente utilizzati nell’industria dei dispositivi medici grazie alla loro eccellente resistenza chimica, prestazioni meccaniche e biocompatibilità.
Tuttavia, le parti in silicone sono notoriamente difficili da prototipare e testare, poiché la maggior parte dei gradi deve essere stampata ad iniezione per raggiungere le loro massime prestazioni.
Alla fine, hanno deciso di implementare il sistema desktop XiP di Nexa3D e Freeform Injection Molding con resina xMOLD prodotto distribuito in Italia da TS Nuovamacut, Gruppo TeamSystem. Questa piattaforma compatta e altamente versatile era l’unica alternativa che soddisfaceva tutti i requisiti chiave, consentendo al contempo a SPT Vilecon di espandersi in nuovi domini basati sullo stampaggio ad iniezione di metalli e ceramiche.
Sviluppo e verifica in 2 giorni di parti in silicone complesse
Con Freeform Injection Molding, SPT Vilecon è stato in grado di offrire a un cliente che stava sviluppando un prodotto in silicone per via endovenosa, una verifica anticipata del design e dei materiali utilizzando strumenti stampati in 3D.
- Verifica anticipata: l’utilizzo di utensili xMOLD stampati in 3D ha consentito al cliente di ottenere parti in silicone stampate ad iniezione in un silicone biocompatibile entro due giorni e di verificare gli aspetti chiave del design e delle prestazioni.
- Iterazioni rapide: allo stesso tempo, sono stati raccolti importanti input di progettazione dai primi test, che potrebbero essere integrati in una seconda iterazione che ha richiesto solo un paio di ore per essere completata. In confronto, gli utensili metallici convenzionali che normalmente sarebbero necessari per questo tipo di verifica avrebbero richiesto più di sei settimane per essere progettati e procurati, e le modifiche necessarie per la seconda iterazione avrebbero richiesto all’officina interna una settimana per essere completata.
- Risparmio di costi e tempo: i costi degli stampi in silicone stampati in 3D per la prima e la seconda iterazione erano inferiori a EUR 2.000 combinati. E il ciclo di progettazione di due giorni era più veloce del 90% rispetto alla velocità raggiungibile con gli utensili metallici convenzionali.
- Scalabilità senza soluzione di continuità: sulla base degli input di progettazione raccolti dalle prime due iterazioni, il design della parte in silicone è stato approvato e la produzione di uno stampo metallico potrebbe essere avviata con piena fiducia nella stampabilità e nelle prestazioni della parte. Gli input di progettazione e gli insegnamenti raccolti hanno consentito all’officina interna di produrre l’utensile metallico entro 4 settimane, senza necessità di iterazioni nello strumento finale.
Condividi l'articolo
Scegli su quale Social Network vuoi condividere