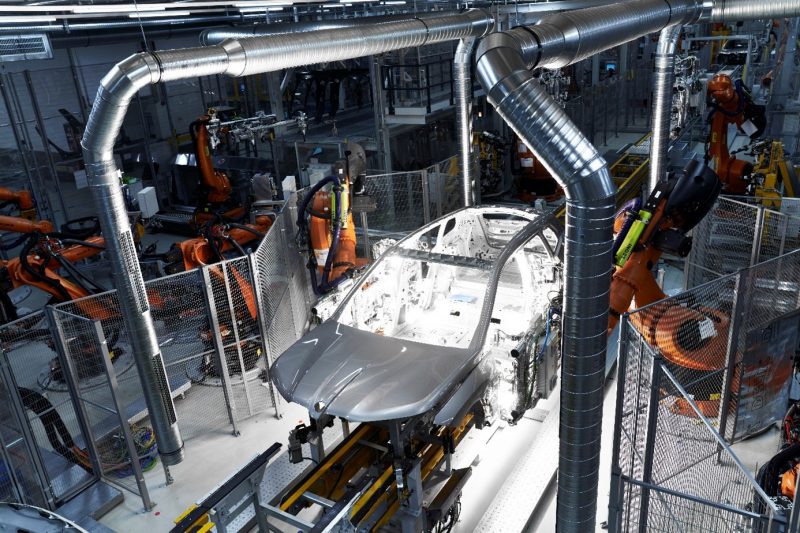
Il contributo dei materiali compositi nella realizzazione di parti strutturali di un’automobile è significativo in termini di alleggerimento e di miglioramento delle prestazioni. In questo articolo presentiamo alcune applicazioni in questo campo premiate con il JEC World Innovation Award 2022.
Il settore dell’automotive è tra i maggiori utilizzatori di materiali compositi. Alcune di queste tecnologie sono state premiate con il JEC World Innovation Award 2022. Qui di seguito vengono prese in esame alcuni dei progetti che hanno ricevuto la candidatura.
Fibra di carbonio per parti strutturali
La prima applicazione strutturale competitiva (CFRTP) è stata presentata da BMW. Si tratta di un nuovo approccio progettuale che utilizza fibra di carbonio senza fine solo per i percorsi di carico, collegando i percorsi di carico con lo stampaggio a iniezione, nessuna produzione di rifiuti in sole 3 fasi di processo, la migliore economia dei compositi di sempre.
L’innovazione si basa su un nuovo approccio progettuale, sulla tecnologia di produzione e sull’integrazione nella carrozzeria dell’auto. La filosofia del design è cambiata: dal design basato sulla superficie al design basato sulla barra, portando a un utilizzo minimo di fibra di carbonio senza fine lungo i percorsi di carico. Le fibre sono perfettamente caricate per pressione e trazione e possono essere ottimizzate per dimensione. Le forze di taglio sono trasmesse dal materiale per stampaggio a iniezione rinforzato con fibre corte. Il processo di stampaggio a iniezione offre una maggiore libertà di progettazione e profondità di integrazione, ad esempio inserti, centraline, cablaggio ecc.
Il processo produttivo richiede solo tre fasi di processo: impregnazione delle fibre, formazione delle barre unidirezionali, stampaggio ad iniezione, tutte completamente automatizzate. Il processo di rifilatura non è più necessario. Si potrebbe realizzare per la prima volta una produzione di compositi a zero rifiuti.
Vantaggi chiave:
- Efficienza dei costi.
- Utilizzo di fibre di carbonio riciclate, riciclabilità del componente.
- Catena di processo di produzione automatizzata semplificata in soli 3 passaggi.
- Nessuno spreco, processo di forma netta.
La sfida dei veicoli elettrici ai materiali compositi
Tucana è il progetto di Jaguar Land Rover in collaborazione con le società briutanniche Broetje Automation, CCP Gransden ltd, Expert Tooling & Automation, Toray International UK, University of Warwick, CFMS.
Tucana è un fattore abilitante per i futuri veicoli elettrici a batteria (BEV) dimostrato dalla riprogettazione dell’intera struttura della carrozzeria posteriore di una Jaguar I-Pace.
A differenza della produzione tradizionale basata su tessuto che utilizza la tecnologia RTM o Autoclave, che non è praticabile per un tempo ciclo ad alto volume (40.000+ unità all’anno) né dal punto di vista del business case, Tucana si è concentrata sull’ottimizzazione dell’uso del materiale e sulla massimizzazione del MPa/kg. Per raggiungere questo obiettivo, l’ottimizzazione della topologia ha contribuito a definire il percorso di carico principale creando così lo scheletro della struttura in cui sono stati posati UD (Uni Directional) in carbonio continuo o fibra di vetro a polimerizzazione rapida. Per dare corpo a questo scheletro e collegare l’UD insieme, sono stati utilizzati CF-SMC (Carbon Fiber Sheet Moulding Compound) e GF-SMC (Glass Fiber Sheet Moulding Compound) per il basso costo, il tempo ciclo rapido e l’elevata libertà di progettazione, in grado di ottenere risultati complessi con forme 3D e complesse caratteristiche di design non facilmente realizzabili con il tessuto tradizionale.
Materiali su misura, parametri di stampaggio specifici e metodo di modellazione proprietario sono stati la chiave del successo.
Vantaggi chiave:
- Struttura del corpo più leggera.
- Riduzione delle emissioni di CO2 come fattore abilitante per l’adozione di veicoli elettrici a batteria.
- Struttura del corpo più rigida che risponde ai requisiti strutturali BEV.
- Conteggio pezzi ridotto – minore energia, spazio a terra, logistica (cioè meno camion).
- Facilità di adozione, conformità con il processo e l’infrastruttura di produzione automobilistica.
Materiali compositi per il tunnel centrale della Jeep Grand Cherokee
Basf, in collaborazione con L&L Products, e Stellantis, ha realizzato il rinforzo in composito del tunnel della Jeep Grand Cherokee modello 2021. Si tratta della sostituzione di un concetto di acciaio ad alta resistenza in un’applicazione critica per la sicurezza utilizzando una pultrusione sovrastampata con materiale termoplastico per ridurre il peso, il numero delle parti, i costi degli utensili e soddisfare le prestazioni.
L&L Products Continuous Composite Systems ha utilizzato il sistema di poliuretano Basf Elastocoat 74850 per la pultrusione continua in fibra di vetro e la poliammide modificata Basf Ultramid 8350 HS Impact Modified per lo stampaggio a iniezione sull’inserto pultruso, creando un nuovo tipo di ibrido. Il processo è altamente automatizzato e non richiede l’apporto umano dal momento in cui l’inserto in fibra continua viene pultruso fino al completamento del pezzo con il sovrastampaggio e i limitatori di compressione.
Vantaggi chiave:
- Nuova applicazione automobilistica ad alto volume per la pultrusione.
- Un nuovo sistema di resina poliuretanica.
- Nuova capacità di progettazione per applicazioni ad alta resistenza.
- Nuovo metodo di simulazione al computer per costrutti in fibra continua – Post Failure.
- Prima per velocità di elaborazione della pultrusione nel settore.
Portiera multimateriale grazie ai materiali compositi
Una porteria multimateriale leggera è stata messa a punto da Hyundai Motor Europe Technical Center in collaborazione con Teijin Automotive Technologies. L’innovativa struttura della portiera in materiale ibrido che utilizza SMC a basso contenuto di COV di nuova concezione e SMC ibrido vetro/carbonio. La portiera è verniciabile sia online che offline e soddisfa tutti i requisiti delle portiere HMG.
Nell’ambito di questo progetto di sviluppo congiunto sono stati sviluppati due innovativi materiali compositi SMC, specificamente ottimizzati per l’applicazione in questo concept di portiera ibrida.
Il pannello esterno utilizza un materiale SMC a bassa densità TCA Ultra Lite modificato. Il pannello interno presenta un materiale SMC ibrido di nuova concezione in fibra di carbonio e vetro.
Per ottenere le prestazioni strutturali richieste, è stato sviluppato un innovativo “anello di rinforzo” interno per garantire percorsi di carico ottimali sia per la rigidità statica che per la resistenza agli urti.
Vantaggi chiave:
- 2,7 kg più leggero del design in acciaio (il totale per veicolo è 9,2 kg).
- Eccellenti prestazioni di robustezza (minori costi di riparazione).
- Stile distintivo con linee di carattere nette (design più accattivanti).
- Costo applicabile alla produzione di massa.
- Verniciabilità online e offline (completamente convalidata con test per entrambe le opzioni).
Stampaggio di materiali compositi a trasferimento di resina
Il progetto di Audi in collaborazione con Mubea Carbo Tech e Apollo Power comporta l’integrazione perfetta di pellicola solare flessibile in componenti in plastica rinforzata con fibre automobilistiche (tetto, cofano eccetera) per applicazioni ad alto volume, utilizzando un processo di stampaggio a trasferimento di resina ad alta pressione.
Con l’infusione di resina poliestere autoestinguente e tessuti in fibra di vetro biassiale sono stati realizzati 3.000 mq di telai compositi, il più grande dei quali è alto 4 metri, lungo 6 metri e pesa solo 250 kg.
L’innovazione comprende l’integrazione di film solari flessibili non incapsulati di Apollo Power (Israele) in parti in plastica rinforzata con fibre utilizzando il processo HP-RTM di Mubea Carbo Tech (Austria).
Il prodotto finale mostra risultati superiori, tra cui una migliore efficienza solare (>200 Wp), un design leggero (minimo il 50% più leggero del tetto solare in vetro standard) e la conformità agli standard di qualità del settore automobilistico. In definitiva, le parti realizzate con materiali sostenibili come fibre naturali (ad esempio, lino), bioresine e pellicole solari possono ridurre enormemente l’impronta di CO2. Inoltre, è possibile realizzare anche forme 3D complesse con un grado di drappeggio più elevato e la tecnologia può essere trasferita ad altri componenti e industrie (ad esempio, ferroviario o aerospaziale).
Vantaggi chiave:
- Design leggero (oltre il 50% di risparmio di peso rispetto al tetto in vetro solare).
- Superficie di classe A con elevata libertà estetica e progettuale.
- La gamma si estende attraverso la pellicola solare applicata.
- Produzione ad alto ciclo con resina a polimerizzazione rapida < 20 min per pezzo.
- Possibilità di combinare film solari flessibili con fibre naturali e bioresine.
Utilizzo delle fibre di lino per compositi rinforzati
Cielini delle automobili rinforzati con fibre di lino leggere sono stati realizzati da Howa-Tramico in partnership con ECO-Technilin, Università della Bretagna del Sud (UBS), INRAe.
L’obiettivo è quello di sviluppare e produrre un nuovo headliner automobilistico con una migliore valutazione ambientale grazie all’uso di fibre vegetali di rinforzo invece di quelle a base di petrolio.
La versione petrolifera del composito integra 7 diversi strati di materie prime, i principali sono l’assemblaggio di schiuma PU con fibre di vetro. Per realizzare il pezzo finale si utilizza un processo di termoformatura e poi alcune operazioni di finitura specifiche come i tagli.
Vantaggi chiave:
- Impatto ambientale migliorato.
- Impatto sulla riciclabilità: riutilizzo dei rifiuti.
- Utilizzo di materie prime non aggressive.
- Utilizzo di un processo di produzione esistente.
- Buona compatibilità tra lino e resina.
Condividi l'articolo
Scegli su quale Social Network vuoi condividere