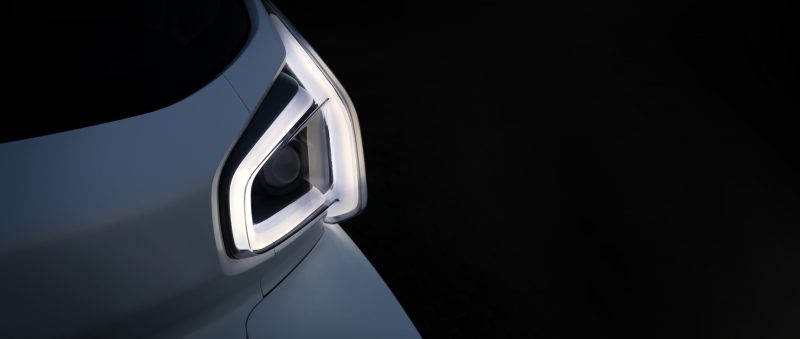
Nella filiera industriale dei trasporti, dall’aerospaziale all’automobilistico, la tecnologia di stampa 3D si sta diffondendo rapidamente come processo finale di lavorazione di un prodotto e non più solo per la prototipazione. Anche in Italia vi sono aziende che si sono negli anni specializzate nella lavorazione tramite questa tecnologia.
Tecnologia stampa 3D: un cluster emiliano
Un esempio importante è la società emiliana Zare, che offre ai propri clienti la possibilità di stampare con la tecnologia 3D più adeguata per ogni prodotto, sulla base della complessità e dei materiali che si vogliono utilizzare, dalle materie plastiche ai metalli. Zare è in grado di realizzare un prodotto dalla sua prototipazione fino alla finitura della fase di lavorazione finale.
Lo scorso agosto, Zare e la società Beamit, entrambe tra i principali partner europei di servizi per la produzione additiva, si sono unite per dar vita a un avanzato partner di produzione nel mercato globale. Questa fusione crea una nuova organizzazione con oltre centro dipendenti e attività distribuite su 5 impianti concentrati in un’area di 40 km tra Parma e Reggio Emilia. La struttura conta anche 4 uffici commerciali in Francia, Germania, Regno Unito e Giappone. Entrambe le società continueranno a operare con i propri marchi, ma le attività convergeranno nel Gruppo Beamit, la cui specializzazione è la fornitura di una gamma completa di materiali, processi, tecnologie e certificazioni per l’aeronautica internazionale, l’aerospazio e la difesa, l’energia, il motorsport, petrolio, gas, e per il mercato dei trasporti.
Questa fusione arriva a seguito della recente integrazione di Pres-X, con il decollo così di un ecosistema-hub nel mondo delle competenze, dei processi e delle tecnologie disponibili sul mercato per traghettare la produzione additiva verso una nuova dimensione industriale e digitale. Obiettivo del gruppo è la semplificazione dei processi per rendere più agili tutte le attività strategiche e cruciali di business con un’offerta di servizi totalmente integrata attraverso partner unici sul mercato.
Beamit SpA opera da oltre ventidue anni nella produzione additiva con polveri metalliche (AM) e dispone di oltre trenta sistemi di additive manufacturing dedicati. La società è un fornitore di componenti AM avanzati in metallo per settori esigenti come quello aerospaziale, automobilistico, energetico e del racing.
Zare srl, attiva dal 1963, è progressivamente diventata un referente di servizi di produzione additiva integrati, dedicando le proprie attività alla produzione di componenti complessi per il settore del motorsport, aerospaziale, automobilistico e oil & gas. Le tecnologie offerte si basano su venticinque diversi tipi di AM, 10 macchine a controllo numerico e una gamma completa di servizi supportati da un team di cinquanta persone altamente motivate e dinamiche.
Pres-X srl fornisce soluzioni altamente qualificate nel post-processing additivo, dalla depolverizzazione alle tecnologie di finitura superficiale di precisione. È stata la prima azienda al mondo a installare un sistema HIQ60, un’apparecchiatura progettata appositamente per i componenti AM che esegue trattamenti termici ad alta pressione, con caratteristiche specifiche per un controllo completo del ciclo termico, consentendo di eseguire contemporaneamente la pressatura isostatica a caldo (HIP) e il trattamento termico.
Con alle spalle oltre 50 anni di esperienza nella meccanica di precisione, ma sempre attenti alle innovazioni di processo, Zare entra nel settore della prototipazione rapida nel 2009 e rapidamente consolida le competenze e amplia il parco macchine inserendo la sinterizzazione dei metalli ed impianti per la prototipazione monolitica a grande formato.
Nel 2011 inaugura l’area dedicata al post-processo, alla finitura dei prototipi e alla preparazione di modelli dentali e medicali. Zare completa l’offerta con i servizi di finitura superficiale particolare, reverse engineering, laminati, fibre leggere. Arriva poi l’industria delle gare sportive, moto e auto,
per cui Zare diviene lo specialista per la produzione di elementi definitivi e funzionali tramite fabbricazione additiva. Per soddisfare il settore del motorsport, la società emiliana adotta una rigorosa pianificazione delle attività, continui test sui materiali per mantenere inalterate le caratteristiche meccaniche tra le diverse produzioni e relazioni dirette con i costruttori di impianti per l’additive manufacturing industriale.
Tra le materie plastiche utilizzate presso gli impianti di Zare, vi è la poliammide 12 PA603-CF caricata con fibra di carbonio e caratterizzata da alte prestazioni. Questo materiale resistente e leggero si distingue per basso peso specifico, buona stabilità dimensionale, elevate proprietà meccaniche e ottima resistenza alla deformazione sotto le elevate temperature. La mescola è stata ottimizzata per ottenere una finitura superficiale liscia senza sacrificare i dettagli a vantaggio delle proprietà meccaniche. Questo materiale si presta ad applicazioni industriali gravose con un HDT di ~177°C, attrezzatura sportiva estrema, componenti per test di aerodinamica e applicazioni che richiedono la massima rigidità e resistenza al calore.
Vi è poi anche la PA6GB40, una poliammide utilizzata nelle applicazioni dove i componenti sono sottoposti ad usura o frizione. Essa garantisce ottimi risultati sia utilizzata per fini prototipali che per la produzione di piccoli lotti e preserie. Rispetto alla PA12 presenta proprietà meccaniche superiori e una maggiore resistenza sia a temperatura ambiente che alle alte temperature. Il grado PA6GB40 parametrizzato dal Centro di Ricerca e Sviluppo di Zare presenta infatti le medesime caratteristiche della PA6 utilizzato con i metodi di produzione tradizionali. I manufatti realizzati con questo grado poliammide tramite la tecnologia di stampa 3D SLS presentano inoltre colorazione bianca completamente analoga a quella dei manufatti ottenuti da PA6GB40 tradizionale e possono essere sottoposti a ripresa meccanica e a verniciatura. Esempi tipici di utilizzo sono boccole, ingranaggi, raccorderia e tutti quei componenti che richiedono buone proprietà meccaniche e resistenza all’usura unita ad un basso coefficiente di scorrimento. L’automotive rimane il settore d’elezione, soprattutto per i componenti utilizzati all’interno dei vani motore.
Flexsinter è invece un polimero sinterizzato che simula le caratteristiche della gomma. Resiste fino 200°C ed è perfetto per contenere fluidi.E’ disponibile un’ampia gamma di colori (nero, blu, giallo, naturale, rosso), tutti con durezza pari a 60ShA. Questo materiale ha una buona flessibilità, un buon recupero elastico ed è durevole anche quando utilizzato nei processi di stampa 3D. Le applicazioni per cui è più adatto sono il settore automobilistico e quello dell’illuminazione.
Tra le materie plastiche usate nella produzione di Zare vi è anche la famiglia dei materiali Ultem, autoestinguenti e resistenti ad agenti chimici. Le caratteristiche del materiale consentono alla tecnologia FDM di essere inserita tra le candidate per la produzione di componenti di gara. Ultem 1010 è una resina FDM ad alte prestazioni che offre alta resistenza termica, chimica e alla trazione. È ideale per applicazioni aerospaziali e nel settore automobilistico. La resina Ultem 9085 è invece un materiale termoplastico ignifugo ad alte prestazioni per la fabbricazione digitale diretta e la prototipazione rapida, ideale quindi per l’industria dei trasporti grazie all’ottimo rapporto tra resistenza e peso e alla certificazione FST (flame, smoke, toxicity). Queste peculiarità lo rendono infatti la scelta ideale per i veicoli aerospaziali, navali e terrestri, per la produzione di parti funzionali a fini prototipali o per componenti definitivi.
Il futuro della mobilità è costruito dalle innovazioni che l’uomo può inserire in un processo produttivo pronto a realizzare componenti originali, esteticamente impeccabili e durevoli nel tempo. In tutto questo la stampa 3d industriale avrà un ruolo sempre più di rilievo assicurando innovazione nelle geometrie, time to market ridotto e test a costi ridotti.
Per dimostrare la propria esperienza nella produzione additiva e nei materiali per il settore del motorsport, la società emiliana ha recentemente realizzato un musetto di una monoposto. Il materiale scelto in questo caso è l’ABS, nello specifico l’ABS-M30, ideale per la modellazione concettuale, i prototipi funzionali, le attrezzature di produzione e per componenti pronti all’uso. Questo grado ABS si caratterizza per l’elevata resistenza alla trazione, all’impatto e alla flessione e garantisce un incollaggio tra gli strati significativamente più resistente di quello dell’ABS convenzionale. I test funzionali sono così più realistici e i pezzi di maggiore qualità, disponibili anche in vari colori. Il musetto è stato realizzato in due parti successivamente assemblate e poi personalizzate mediante la stampa e l’applicazione di flap e altre parti complementari, così da evidenziare i vantaggi e le potenzialità della tecnologia additiva.
Galvanostegia: plastica e metallo insieme
Le potenzialità della stampa 3D nel settore automotive sono ben spiegate da Stefan Holländer, Managing Director EMEA di Formlabs, che sottolinea come questa tecnologia consenta una elevata personalizzazione, bassi costi e tempi di produzione ridotti. Le tecnologie di stampa 3D possono, tra l’altro, essere combinate con i processi convenzionali, come ha fatto Volkswagen per la nuova edizione del suo Microbus del 1962. La forma insolita e intrecciata dei cerchioni in alluminio di questo mezzo richiedeva una combinazione di cerchi appositamente studiati. I coprimozzi sono stati prima stampati in 3D in collaborazione con Formlabs utilizzando il processo SLA e quindi zincati per ottenere l’aspetto e la sensazione di parti metalliche reali.
Tecnologie e materiali 3D desktop innovativi consentono ai team di ingegneria e progettazione di ridurre drasticamente la distanza tra idea e prodotto finale. I prototipi di singoli elementi interni, come un cruscotto, possono essere stampati direttamente sul posto in poche ore, testati per l’idoneità e, se necessario, adattati immediatamente. Le nuove resine sintetiche speciali per la prototipazione consentono di ridurre i tempi di produzione di oltre il 70%. È quindi possibile accelerare i cicli iterativi e rafforzare il processo di sviluppo del prodotto, offrendo un enorme potenziale per l’industria automobilistica, dove una convalida rapida è essenziale.
Stefan Holländer sottolinea anche quanto la stampa 3D offra nuove opzioni per la forma e il design e la personalizzazione di piccole quantità. La stampa 3D può infatti essere utilizzata per produrre parti personalizzate in piccole quantità a costi accessibili senza la necessità di personalizzare un’intera linea di produzione o di manodopera estesa.
Ad aprire svariate nuove possibilità per l’industria automobilistica, come già detto, non è solo l’uso di nuove tecnologie di stampa 3D innovative, ma anche la loro combinazione con i processi convenzionali. Formlabs nelle sue lavorazioni è in grado di combinare parti stampate con polimeri e processi come fusione a cera persa, fusione a sabbia o fusione diretta a bassa temperatura per produrre parti metalliche specifiche con finiture di superficie particolari. Combinando la stampa 3D con altri processi, è possibile sfruttare le innovative tecnologie di stampa 3D con polimeri per soddisfare requisiti come time-to-market, riduzione dei costi, facilità d’uso, precisione e iterazioni rapide per creare altri materiali più sofisticati come il metallo.
Il processo di galvanostegia consente di combinare parti in plastica stampate in 3D con le proprietà meccaniche e chimiche superiori dei metalli. In questo processo, ha spiegato Stefan Holländer di Formlabs, uno strato sottile del metallo desiderato viene depositato elettrochimicamente sulla superficie della parte stampata in 3D. Il risultato è una vera superficie metallica. Oltre a conferire un aspetto metallico, la galvanostegia rafforza in modo significativo anche la parte sottostante e migliora la resistenza del materiale a usura, esposizione ai raggi UV e corrosione. La resistenza alla trazione delle parti stampate in 3D SLA viene così aumentata in media di tre volte, la resistenza alla flessione di quasi dieci volte e la rigidità di quattro volte.
Un ulteriore vantaggio è rappresentato dal gran numero di metalli che possono essere utilizzati per la galvanostegia e la conseguente varietà di possibili usi e applicazioni per le parti finite. Tra le altre cose, il processo di raffinamento consente di produrre parti precise e relativamente economiche da oro, nichel e rame, con ogni metallo che offre i suoi vantaggi specifici. Ad esempio, la raffinatezza dell’oro è l’ideale per ottenere un aspetto straordinariamente nobile con costi dei materiali relativamente bassi, poiché non è l’intera parte ad essere realizzata in oro, ma solo lo strato superiore, con lo stesso risultato ottico. Le parti raffinate con nichel sono estremamente resistenti alla corrosione, mentre le superfici in rame hanno un’elevata conducibilità elettrica. La superficie metallica può quindi essere lucidata, spazzolata, sabbiata o rivestita come qualsiasi superficie metallica sottile, a seconda delle esigenze di progettazione e dell’uso previsto. Nel caso dei coprimozzi per il microbus Volkswagen, le superfici in rilievo sono state lucidate a specchio, mentre la superficie goffrata dietro il logo Volskwagen è rimasta opaca, creando un sottile contrasto.
La galvanostegia dei modelli in plastica stampati in 3D può essere utilizzata in tutte le aree della produzione automobilistica in cui le superfici metalliche sono fondamentali. Inoltre, è una soluzione adatta soprattutto per le parti di produzione che devono combinare le proprietà esterne del metallo con il minor peso possibile. L’uso della stampa 3D cava o basata su griglia come base consente un ulteriore risparmio di peso.
a cura di Valeria Mazzucato
Condividi l'articolo
Scegli su quale Social Network vuoi condividere