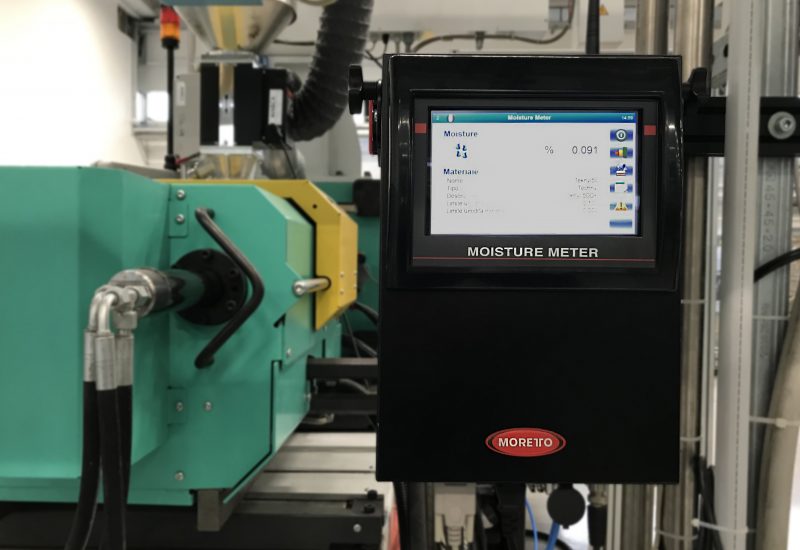
Attraverso l’utilizzo di sistemi all’avanguardia, come il sistema di deumidificazione dei polimeri tecnici fornito da Moretto, Marca Group è in grado di gestire in maniera ottimizzata tutte le fasi del processo produttivo, seguendo la logica propria della quarta rivoluzione industriale.
Spostare il centro dell’isola di lavoro, fino ad ora rappresentato dalla singola pressa a per stampaggio a iniezione, verso un più complesso sistema di gestione delle risorse, utilizzando strumenti innovativi in grado di governare l’intero processo produttivo attraverso la raccolta e l’analisi dei dati provenienti dai vari impianti, secondo i dettami dell’Industria 4.0. Questa la strategia messa in atto da Marca Group che, da quasi cinquant’anni, fa dell’innovazione uno dei propri punti di forza nell’approccio al cliente. Presente sul mercato dal 1971 grazie all’esperienza maturata dal fondatore Adriano Parini presso uffici tecnici e attrezzerie della zona, la società milanese ha iniziato le proprie attività con la costruzione di stampi per la formatura di materiali termoplastici, trasferendo nel 1979 la propria sede amministrativa e produttiva a Nerviano, nell’hinterland del capoluogo lombardo, attuale sede operativa. Tra i passi più importanti compiuti negli anni, oltre all’ottenimento delle certificazioni DNV per lo stampaggio (in conformità alla UNI EN ISO 9002), UNI EN ISO 9001:2000 e ISO/TS-16949:2002, spiccano l’apertura nel 2002 della sede produttiva in Romania, l’inaugurazione nel 2016 del nuovo polo produttivo italiano da 6 mila metri quadrati e, nel 2018, di uno stabilimento in Moldavia.
“Oggi l’azienda – spiega Massimo Parini, Production Manager di Marca Group – vanta un organico d’una sessantina di persone in Italia e 300 in Romania, impegnate nella produzione di articoli tecnici per clienti nazionali ed internazionali, che assemblano i prodotti Marca destinati alle più importanti case mondiali nei settori dell’industria automobilistica, informatica, elettrotecnica e degli elettrodomestici”.
Prodotti realizzati attraverso l’utilizzo di un ampio parco impianti, composto da 38 presse per stampaggio a iniezione installate nello stabilimento di Nerviano e 60 in quello rumeno, da 10 a 400 tonnellate, in grado di trasformare circa 1200 tonnellate annue di termoplastici come PA, PE, PP, PC, ABS, PS, PMMA o PET, oltre che termoindurenti epossidici, fenolici e a base poliestere, attraverso un apposito reparto equipaggiato con differenti macchinari per lo stampaggio ad iniezione (da 50 a 150 tonnellate) e compressione.
La soluzione giusta
In questo contesto s’inserisce il Moisture Meter che Moretto ha fornito a Marca Group, un dispositivo innovativo, capace di misurare in-line il reale contenuto d’umidità residua del granulo (in ppm), controllando e gestendo in close-loop il processo di deumidificazione, al fine di garantire una produzione di qualità, con rilevanti risparmi energetici. Un dispositivo frutto della grande esperienza maturata dall’azienda di Massanzago (PD) nella progettazione e realizzazione di sistemi dedicati alla trasformazione delle materie plastiche, attraverso soluzioni competitive, vantaggiose nel medio periodo e personalizzate secondo le esigenze di ogni singola realtà industriale.
Moisture Meter misura il livello di umidità residuo e controlla che il polimero sia opportunamente deumidificato prima del processo di trasformazione.
L’esclusiva tecnologia Power-Peak analizza le caratteristiche dielettriche del granulo e rileva l’esatto contenuto di acqua presente nel polimero, senza alcuna ulteriore taratura off-line. Il dispositivo è dotato di una straordinaria capacità di misurazione in grado di rilevare da 3.000 sino ad un minimo di 15 parti per milione (ppm), con un grado di precisione di ±3 ppm e un range di temperatura 20-180°C.
“Moisture Meter è un dispositivo molto apprezzato da parte della nostra clientela la quale ne apprezza la tecnologia, l’assoluta precisione, oltre che la facilità di utilizzo e di condivisione dei dati.” – afferma Antonio Gallo, Domestic Sales Manager di Moretto – “Dal 2017 abbiamo introdotto sul mercato un’importante evoluzione del prodotto dal nome “Moisture Meter Manager”, il quale integra il dryer in un sistema adattivo come delineato dall’Industria 4.0”. – continua.
Moisture Meter Manager è costituito dai dispositivi MM Box, MM Crown e dal controllo Manager: il primo, di cui abbiamo parlato poco fa, è posizionato alla base della tramoggia, misura il livello d’umidità residuo e controlla che il polimero sia opportunamente deumidificato prima del processo di trasformazione, garantendo la qualità del granulo secondo i requisiti richiesti, evitando così il rischio d’incappare in scarti di produzione.
Il dispositivo MM Crown, invece, installato all’ingresso della tramoggia, rileva il livello dell’umidità iniziale del granulo, permettendo al sistema di prevedere esattamente il processo di deumidificazione e di gestire, inoltre, tutti i parametri per ottenere l’esatta umidità finale del polimero in uscita, rilevata dal dispositivo MM Box, posizionato sotto la tramoggia. La misurazione della differenza tra l’umidità iniziale e quella finale del granulo permette a Moisture Meter Manager di gestire autonomamente le condizioni di lavoro dell’essiccatore, massimizzando le performance di processo, sfruttando solo l’energia strettamente necessaria.
Sistema adattivo automatico
«In questo modo si crea un close-loop perfetto che integra il dryer in un sistema adattivo completamente automatico. Il dispositivo è dotato di un’interfaccia operatore touch-view da 10” HD a colori, semplice da programmare e object-oriented, capace di gestire fino a 12 tramogge, ognuna equipaggiata con sensori Crown e Box – aggiunge Gallo – Moisture Meter Manager può essere interconnesso con sistemi Ethernet, Serial RS 485, USB e Mowis Supervisor, fornendo dei report per ogni lavoro, archiviandoli per 30 giorni a disposizione anche per essere eventualmente stampati».
Il nuovo dispositivo di casa Moretto crea così una perfetta deumidificazione di tipo on-demand, basata sulle reali esigenze di essicazione del polimero e capace di gestire le variabili, interne ed ambientali, che interferiscono con il livello d’umidità del polimero stesso. Uno strumento, dunque, che punta nella direzione della cosiddetta Fabbrica Intelligente 4.0, con impianti e sistemi interconnessi e la disponibilità d’una notevole mole di dati da elaborare e condividere, al fine di raggiungere livelli sempre più elevati di efficienza produttiva.
Moisture Meter è integrato con il software di gestione di processo, basato sul protocollo di comunicazione universale OPC-UA.
I risultati
«Grazie all’utilizzo del Moisture Meter siamo così in grado di mantenere il processo sotto controllo, riducendo a zero gli scarti, avendo al contempo a disposizione tutte le informazioni, in tempo reale, da analizzare e da gestire. Il passo successivo sarà poi quello d’anticipare la nascita di un problema, cercando di prevedere l’andamento nelle relazioni di tutte le variabili che porterà ad un certo tipo di risultato – ha voluto spiegare Parini – Il rapporto intrapreso con Moretto è ormai lungo e duraturo, essendo partiti con l’impianto di deumidificazione centralizzato, per poi arrivare al trasporto e all’essicazione a bordo macchina, avendoci affiancato, nel corso degli anni, per ogni nostra necessità produttiva, consentendoci di crescere molto in termini di efficienza e competitività».
Infatti, come ha tenuto a sottolineare Parini, da quando l’azienda s’è insediata nello stabilimento di Nerviano, ha sempre lavorato a ciclo continuo, senza mai fermarsi, ricevendo feedback molto positivi da parte del mercato. Feedback che hanno indotto Marca Group ad investire in nuova tecnologia, con soluzioni come l’innovativa macchina per la tomografia industriale, in arrivo nei primi mesi del prossimo anno, a completamento del parco strumenti metrologici, indispensabile sia per il controllo dimensionale, che di processo, consentendo all’azienda milanese di vedere, all’interno dei pezzi, eventuali inclusioni, bolle d’aria o soffiature, senza più dover operare controlli distruttivi.
Logiche 4.0 per lo stampaggio a iniezione
«L’azienda ha sempre avuto la vocazione all’innovazione, che l’ha portata ben presto all’implementazione delle logiche 4.0 all’interno degli stabilimenti, al fine di ottimizzare tutte le fasi del processo. Così, un paio d’anni fa abbiamo deciso d’installare dei monitor, dislocati nel sito di produzione, che indicano l’elenco delle operazioni da fare, in tempo reale, sulla base dello stato di avanzamento lavori, oltre che l’efficienza produttiva, l’utilizzo e la saturazione delle macchine, con la visualizzazione degli scarti interni e di tutto quanto utile alla pianificazione del processo – afferma Massimo Parini, Production Manager di Marca Group – Abbiamo poi altri pannelli che indicano l’andamento delle varie presse, con la visualizzazione in real-time dei parametri di settaggio e di funzionamento delle macchine per lo stampaggio a iniezione, a disposizione degli operatori per una gestione ottimizzata di tutte le fasi di lavorazione, oltre che dei pianificatori, per l’analisi dei dati in uscita dagli impianti, diretti al nostro sistema gestionale. Ed anche gli stampi hanno al loro interno tutto un sistema di sensoristica che ci invia feedback sui vari stati del sistema, dai riscaldamenti ai raffreddamenti delle camere e dell’iniezione».
Ma gli aspetti innovativi del processo passano anche attraverso la recente creazione di tutta una serie d’istruzioni e documenti, normalmente allegati in forma cartacea alle macchine per stampaggio a iniezione (dalle distinte base, ai piani di controllo delle commesse), ora in formato elettronico, ben visibili a monitor, integrandoli anche con alcuni tutorial, appositamente concepiti per garantire una formazione qualificata agli operatori, senza la necessità di fermare gli impianti (che funzionano 24 ore su 24) per frequentare specifiche sessioni di training.
«Nel momento in cui si rende necessario effettuare un intervento o una regolazione su un impianto, attraverso questi tutorial il tecnico può vedere in anteprima le operazioni che deve effettuare, così da essere pronto ad intervenire nella risoluzione di una problematica; appositi corsi formativi ad opera di enti certificati, poi, vengono regolarmente organizzati, per mantenere il nostro personale sempre aggiornato sulle nuove tecniche produttive disponibili sul mercato – ha proseguito – La raccolta di questa grande mole di dati, dunque, diventa centrale per il buon funzionamento del processo di produzione, oltre che indispensabile per l’analisi di tutte le fasi che portano alla creazione del prodotto finito, secondo i dettami dell’Industria 4.0».
Condividi l'articolo
Scegli su quale Social Network vuoi condividere