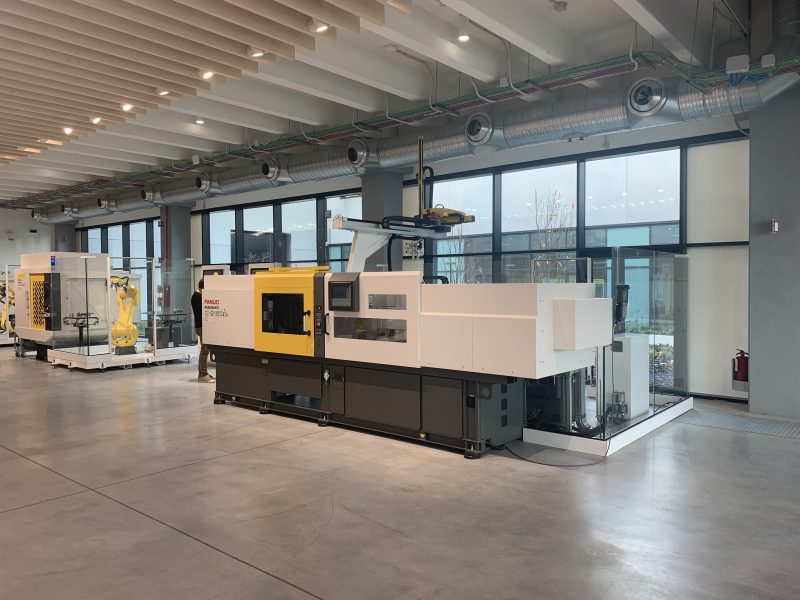
Open house dedicata allo stampaggio a iniezione presso il quartier generale di Fanuc Italia. In mostra le presse “full electric” Roboshot caratterizzate da elevata precisione e bassi consumi energetici. Implementati software e dispositivi di ottimizzazione del ciclo di produzione.
La recente open house presso la sede Fanuc Italia di Lainate (Milano) è stata l’occasione per prendere visione delle caratteristiche tecniche e prestazionali delle presse per stampaggio a iniezione Roboshot e dell’automazione fornite dalla casa costruttrice giapponese.
Come sottolineano i tecnici, le presse Fanuc, ad azionamento totalmente elettrico, sono macchine utensili dedicate alle plastiche, soprattutto grazie a un CNC, impiegato anche nella tornitura e nella fresatura, che suddivide il processo di stampaggio in quattro percorsi indipendenti che operano in parallelo: iniezione, plastificazione, chiusura, estrazione. A ciò si aggiungono due motori per l’accostamento del carro e la regolazione dello spessore. Fondamentale il ruolo della componente elettronica che accresce la velocità di esecuzione e la precisione del processo.
Durante l’open house, i visitatori hanno potuto osservare una pressa Roboshot α-S150iA equipaggiata con robot antropomorfo Fanuc M-10iA e robot cartesiano Fanuc Compact 1 (per pezzi fino a 5 chilogrammi di peso) equipaggiato con elettronica Fanuc. Il programma della macchina viene collegato a quello del robot che può prelevare le sue sequenze in modo autonomo. È stato inoltre integrato il software dedicato alla manipolazione del pezzo, che consente lo svincolo del robot, l’azzeramento ed il restart ciclo direttamente dal pannello di controllo della macchina. È disponibile anche il robot di taglia maggiore Compact 2 per pezzi fino a 7 chilogrammi. In alcuni casi sono state realizzare soluzioni customizzate. Una seconda pressa, una Roboshot α-S100iA, equipaggiata con robot antropomorfo, ha effettuato prove di stampaggio con prelievo e manipolazione del pezzo.
Le funzioni specifiche
La gamma di presse Roboshot è composta da macchine con forza di chiusura dalle 15 alle 500 tonnellate, quest’ultima presentata al K 2019. Nel 2022 è prevista la presentazione della nuova generazione di presse.
Le macchine Roboshot sono dotate di speciali funzioni che ne migliorano le prestazioni, aumentano la qualità dei pezzi stampati e diminuiscono il consumo di energia. Fra questi c’è il Clamp Force Adjustment che consente di controllare e regolare automaticamente la forza di chiusura minima, garantendo in tal modo maggiore sicurezza ed eliminando la necessità di regolazioni manuali. Dopo aver impostato la forza di chiusura e con processo in funzione, il sistema monitora la coppia sulla ginocchiera durante la fase di mantenimento: se la forza è insufficiente o eccessiva, il dispositivo procede a stabilizzarla. I benefici principali sono l’azione di degasaggio, la riduzione dei tempi di avviamento e dell’usura della meccanica e dello stampo, la qualità superficiale dei pezzi, il minor consumo energetico.
Un’altra funzione interessante è quella che analizza il Back Flow che consente di capire quando la valvola di iniezione è chiusa o aperta e se c’è usura del componente. Può quindi essere usata anche a scopo predittivo, evitando così un fermo macchina o una rottura. A questo proposito, sarà predisposta a breve una pagina dedicata alla manutenzione predittiva per diverse parti meccaniche come viti, unità di iniezione, cinghie ecc.
La funzione di dosaggio preciso effettua una decompressione del materiale a fine dose (eliminando il problema del “filo” della materozza), oppure una compressione del materiale alla fine del dosaggio, preparando lo step successivo. A questa funzione si aggiunge il calcolo del volume della stampata che mantiene costante il volume della dose e si adatta nel caso ci sia un cambio di posizione del cuscino, così che il peso del pezzo rimanga invariato.
Controllo intelligente
AI Metering Control attiva il controllo intelligente per evitare flusso di volume non controllato durante la fase di plastificazione; campiona una curva di dosi ottimali per ripeterla nel tempo, stabilizzando il tempo di permanenza del materiale nella camera di plastificazione. La macchina adatta i giri della vite alla contropressione di plastificazione, conservando lineare il tempo di arretramento della vite, soprattutto nel caso di utilizzo di un misto di materiale vergine e rigenerato, spesso non omogeneo. Tra i vantaggi, un volume di plastificazione costante per materiali a bassa viscosità, riduzione delle variazioni di peso delle parti, possibilità di evitare bolle e altri difetti e qualità delle parti più elevate, con minori scarti.
a cura di Paolo Spinelli
Condividi l'articolo
Scegli su quale Social Network vuoi condividere