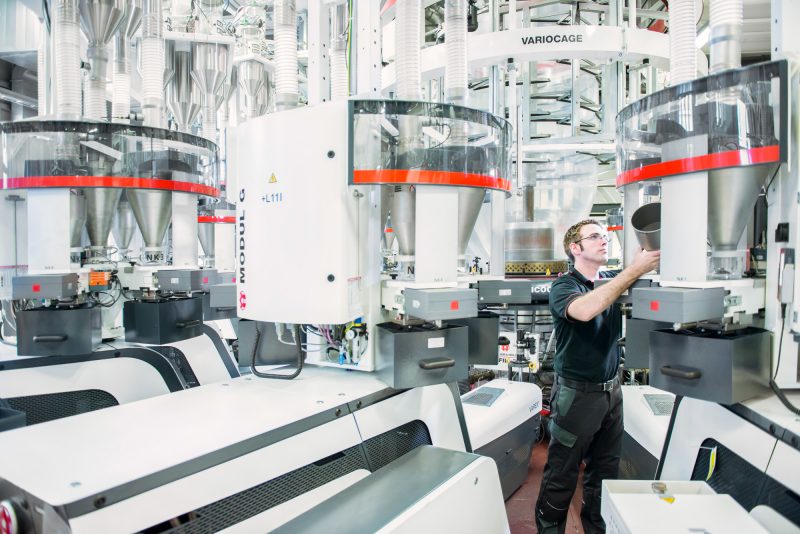
Nonostante il difficile periodo che sta attraversando il comparto produttivo, a causa dell’emergenza pandemica, Windmöller & Hölscher continua a soddisfare un’elevata richiesta di mercato, grazie alla qualità della propria offerta nel campo dell’estrusione.
Centocinquant’anni d’esperienza, passione, professionalità e voglia di offrire soluzioni tecnologicamente avanzate in un comparto, come quello delle materie plastiche, che si dimostra in continua evoluzione. Dal 1869 Windmöller & Hölscher è presente sul mercato grazie all’elevato know-how acquisito nell’ambito della produzione di macchinari e linee complete per la produzione di imballaggi flessibili. La gamma di prodotti offerta oggi dall’azienda di Lengerich, in Germania, comprende impianti ad alte prestazioni per l’estrusione, per la stampa, per la trasformazione di film, per i sacchi di carta e, attraverso la consociata Garant, anche macchinari per la realizzazione di sacchi di carta di dimensioni più piccole (sacchetti per farina e zucchero), e macchine di seconda mano. Un organico di oltre 3 mila dipendenti è impegnato nella realizzazione di soluzioni ottimali per ogni specifica esigenza dei clienti, offrendo loro tutta la tecnologia disponibile da un unico fornitore, oltre che servizi di consulenza e ingegnerizzazione ad opera di tecnici esperti, fino alla consegna di progetti, impianti di alta qualità e linee di produzione complete per l’imballaggio.
La presenza in Italia
Ad oggi le macchine di W&H in funzione solo oltre 10.000, in oltre 130 paesi del mondo, tra cui l’Italia, rappresentata dalla filiale Windmöller & Hölscher Italiana S.r.l., con sede a Lodi, a completa disposizione della clientela con un’ampia gamma di servizi di assistenza tecnica e commerciale.
«La nostra filiale si occupa del mercato nazionale per le divisioni carta, stampa ed estrusione, oltre che di Garant e devo dire che in tutti i rami la situazione di mercato è molto positiva – ha affermato Daniele Cerizzi, Amministratore Delegato di W&H Italiana – Siamo in realtà un po’ stupiti del fatto che l’estrusione, in particolare, sia così in ascesa, nonostante tutti i dibattiti attorno alla plastica e alla sua presunta dannosità per l’ecosistema: certamente gli Stati Uniti in questo momento sono il mercato trainante, ma anche il nostro paese sta garantendo numeri davvero importanti, così come la Germania, la Cina e l’India».
Le tendenze del mercato
Questo, nonostante il difficile periodo che il comparto manifatturiero sta attraversando a causa dell’emergenza sanitaria indotta dal virus Covid19, che ha messo un po’ tutti i settori industriali in difficoltà. L’azienda di Lengerich in questo momento è oberata di lavoro e di commesse, con tempi di consegna che arrivano anche a superare l’anno, estrusione in primis, per tutti i tipi di macchine, dal bolla a 3 strati per stretch hood al 5 strati per accoppiamento, fino al film barriera e all’MDO (Machine Direction Orientation), sia per gli stiri in applicazioni igieniche (breathable), che per il PET replacement, ovvero la possibilità di avere un mono-prodotto in polietilene che sostituisca questo polimero, pur mantenendone le medesime caratteristiche.
«In questo ambito stiamo facendo molte prove con i clienti presso la sede centrale in Germania, anche utilizzando telecamere installate nei pressi dei vari impianti di estrusione dedicati nel laboratorio di test, così da sfruttare le connessioni in remoto, nel rispetto dei protocolli sanitari anti Covid-19 – ha proseguito Cerizzi – La tendenza del mercato, circa la sostituzione del PET con il PE, è infatti molto forte e noi siamo stati tra i precursori nella costruzione degli impianti MDO, ovvero sistemi brevettati a 10-12 rulli riscaldati, che stirano il film bolla in senso macchina fino a 10 volte lo spessore iniziale, utilizzando formulazioni speciali e materiali specifici, per consentire un netto aumento delle caratteristiche meccaniche del film».
E, tra i vantaggi nell’accoppiamento di un PE con un altro PE c’è il fatto che il materiale finale diventa completamente riciclabile. La stessa macchina, inoltre, utilizzando formulazioni con il 50% di plastica a bassa densità e con il restante 50% di carbonato di calcio, rende il film traspirante, utilizzabile così nella realizzazione di pannolini, dove W&H vanta una forte presenza di mercato.
Personalizzazione degli impianti
Qualora, poi, vi fossero particolari esigenze, l’azienda è anche in grado di personalizzare le macchine seguendo determinate specifiche di ogni singolo cliente, al fine di soddisfare tutte le aspettative.
Da non sottovalutare l’aspetto legato alla sostenibilità, verso il quale Windmöller & Hölscher si sta concentrando, sviluppando impianti capaci di processare anche biomateriali.
«All’interno del laboratorio in Germania stiamo facendo svariati test mediante l’utilizzo di 5 macchine in bolla ed una in cast, a disposizione dei clienti, così che potranno presto toccare con mano la qualità delle nostre realizzazioni anche in questo campo – ha concluso – In futuro c’è anche la volontà di partecipare ad un’edizione della fiera milanese Plast (quando sarà possibile), nella quale credo molto, perché sono convinto della sua efficacia come richiamo di visitatori e per avere un contatto diretto tra produttori e consumatori di un settore che, ad oggi, in Italia è in costante e continua evoluzione».
Soluzioni all’avanguardia
Rivolgendo lo sguardo alle linee di estrusione più tradizionali del film a 3-5-7 strati, Windmöller & Hölscher spinge molto sulla ricerca tecnologica, offrendo alla clientela tutta una serie di nuovi accessori per il retrofit anche su macchine esistenti, assecondando le richieste di un mercato che, in questo momento, sta andando molto bene.
Da evidenziare, in particolare, i sistemi Profile Booster, che mandano la macchina a spessore ottimale in maniera rapida qualora dovesse fermarsi per qualsiasi ragione, oppure se il cliente eseguisse cambi di lavorazione sostanziali.
Il costruttore fornisce anche il dispositivo turbo-start, presentato alla fiera K di Duesseldorf nel 2019, che offre la possibilità, nel momento in cui si cambia completamente lavoro o si rompe il pallone, di andare in produzione con un indirizzamento del materiale in automatico, senza la necessità che l’operatore vada a tagliare il film e a metterlo in misura.
Infine c’è il Purge Assist, indispensabile quando si passa da una formulazione ad un’altra e c’è bisogno di pulire la testa, con una rapidità di molto superiore rispetto ai sistemi tradizionali.
Interessante anche il nuovo sistema Ruby d’interfaccia delle macchine W&H con la piattaforma digitale del cliente, legata alle logiche dell’Industria 4.0. I tecnici e gli specialisti di W&H hanno lavorato molto su questo aspetto negli ultimi anni, installando il sistema su tutti gli impianti prodotti: poi, attraverso differenti software, ognuno dedicato ad uno specifico campo d’applicazione (estrusione, stampa, carta, eccetera), la macchina mette a confronto una moltitudine di dati ed è in grado di fornire agli operatori tantissimi output, che vanno dal consumo istantaneo a quello giornaliero di energia elettrica, dalla produzione durante un turno al numero di volte che l’impianto è andato fuori spessore o altre informazioni utili a chi gestisce il ciclo produttivo, per consentirgli di adottare le opportune azioni, volte al miglioramento e al controllo completo della produttività.
Questo aspetto è molto apprezzato in Italia, dove le aziende possono sfruttare le potenzialità offerte dai protocolli della quarta rivoluzione industriale, con agevolazioni fiscali per il 4.0, che sicuramente hanno dato una decisa spinta verso l’adozione di questi protocolli. Gli impianti Windmöller & Hölscher, in generale, vengono offerti al cliente partendo da un’ampia fascia di soluzioni che abbiamo sviluppato in base alle portate e all’accessoristica necessaria, capaci di coprire la maggior parte delle necessità in termini di volumi e lotti produttivi.
Condividi l'articolo
Scegli su quale Social Network vuoi condividere